DIF Dental Implants production
MAIN REQUIREMENT FOR PRODUCTION
The main indicator of a high level of production is the quality of the manufactured product. To provide our clients with necessary high level quality product we organized a special department consisting of professionals with experience in turning and medical production for more than 25 years, who have at their disposal advanced measuring and optical equipment that allows control all the nuances of the production process: material, product parameters, tolerances, surface treatment, sterilization and final packaging of the product.
The DIF Dental Implant system specialists constantly monitor the quality of the products at all stages of the manufacturing process and production, they draft instructions for all manufactured parts and ensure that all product lines meet the requirements of the International Organization for Standardization (ISO 9001, ISO 13485, 93/42 EEC).
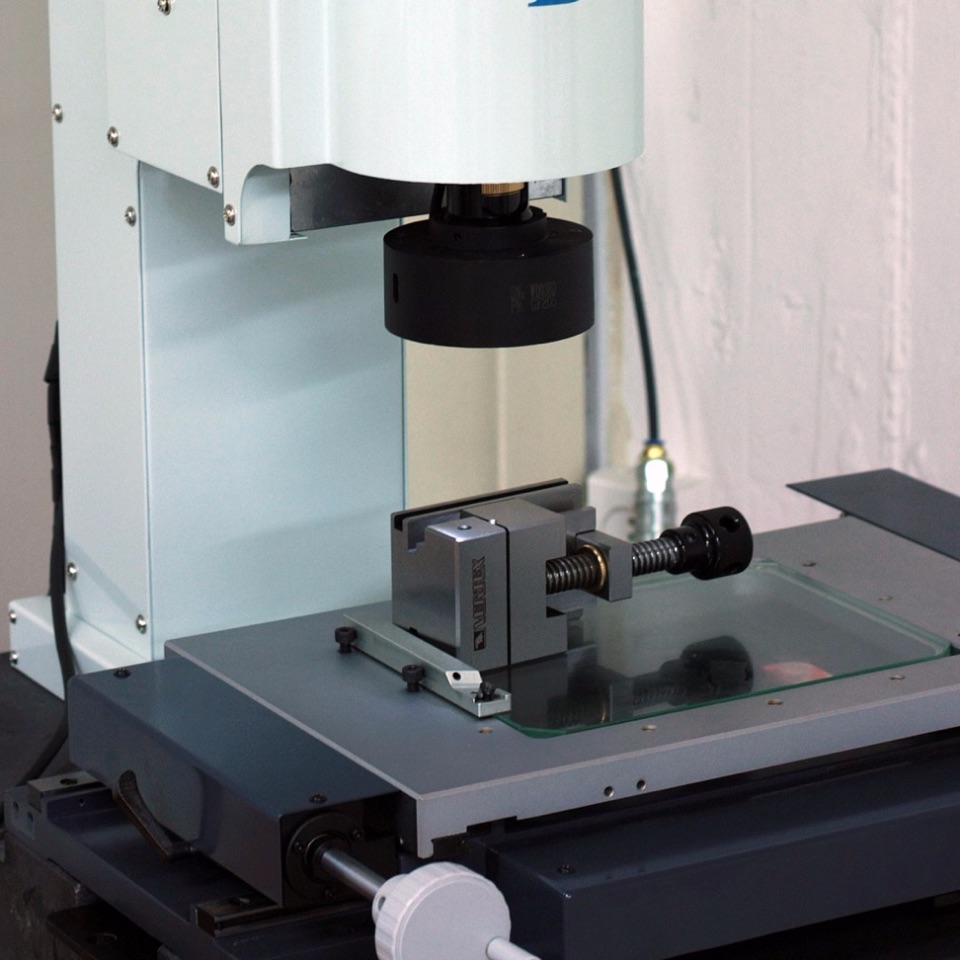
LASER MICROSCOPE
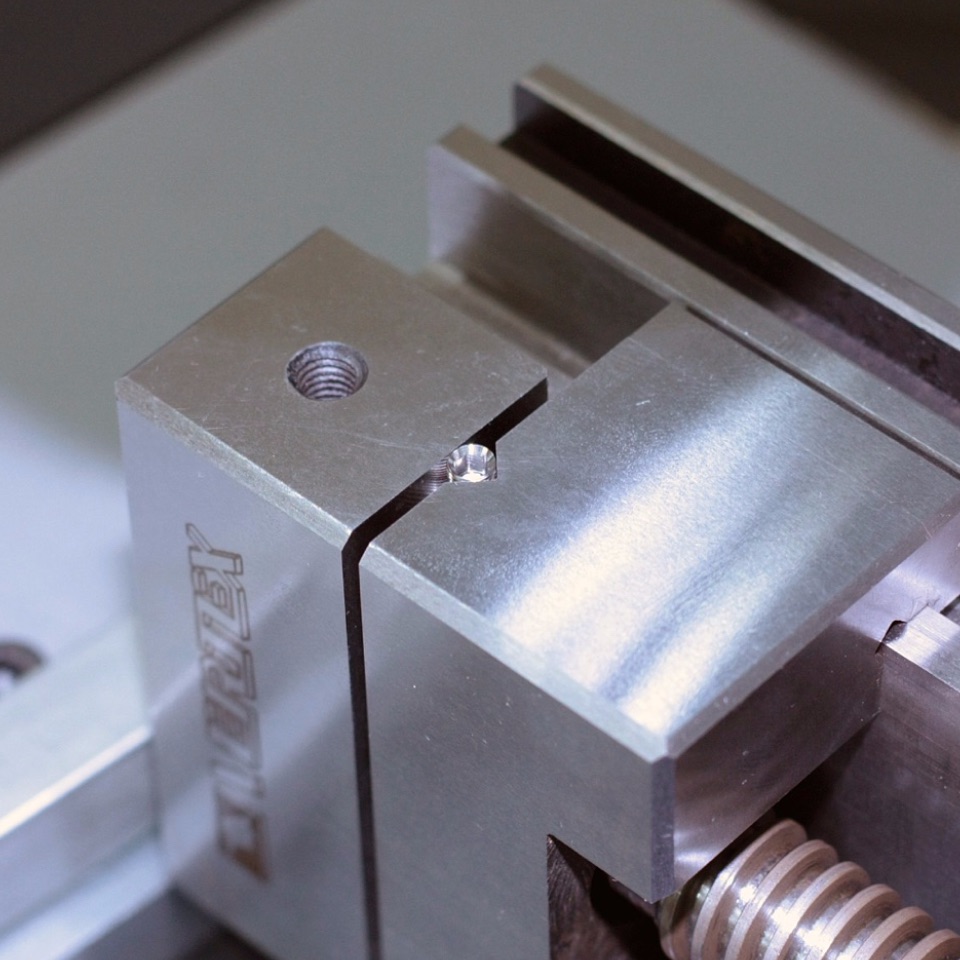
IMPLANT IN INSTALLATION
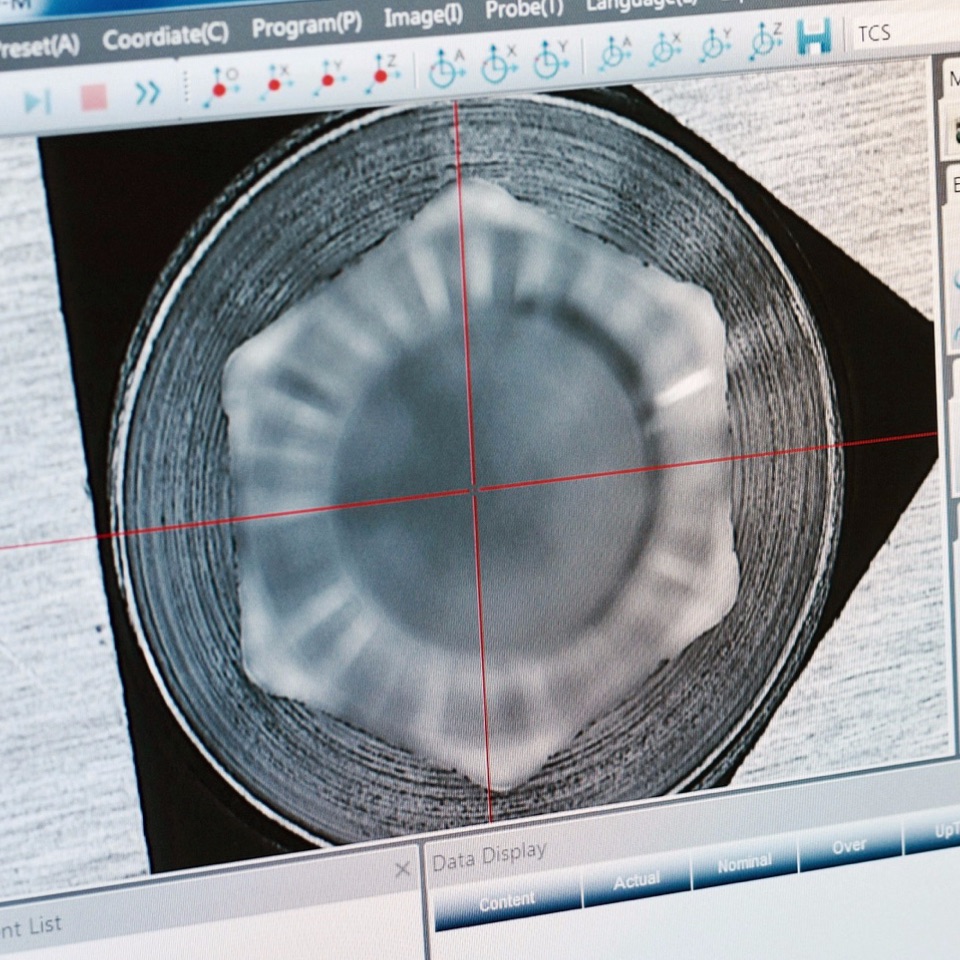
CHECKING ACCURACY CHARACTERISTICS
RAW MATERIAL
Titanium and its alloys are the main materials for implant manufacturing in the world dental practice. Titanium is compatible with other inert metals when in the body, without causing galvanic effect.
TITANIUM FOR IMPLANTS
Titanium alloy grade Ti 6Al – 4V ELI
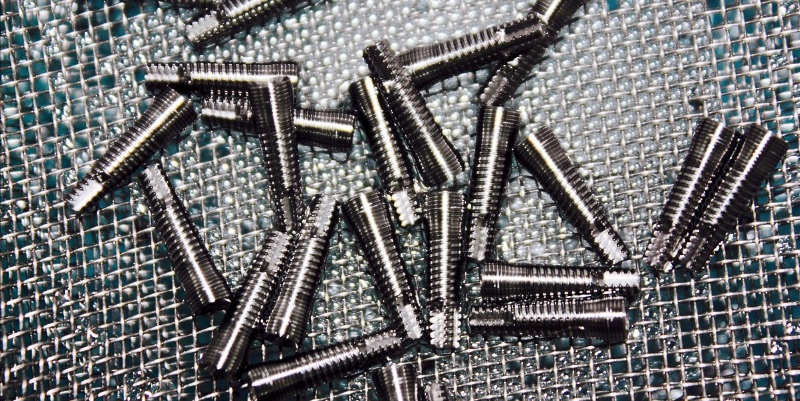
IMPLANT SURFACE TREATMENT
The implant surface must meet certain requirements for effective osseointegration in the human jaw. Today there are about 10 types of implant processing, however, in the world practice, mainly two types are used: SLA and RBM.
SLA is an abbreviation for Sand-blasted, Large grit, Acid-etched (coarse sandblasting and acid etching). During SLA treatment, the implant surface is sandblasted, i.e. bombarded with liquid-metal mass, and then etched with acid to give it a roughness. Various materials are used as sand.
The most common bombardment materials are AL2O3 (aluminum oxide), TiO2 (titanium oxide), RBM (calcium phosphate) and BCP - biphasic calcium phosphates (calcium phosphate apatite). Particle size, pressure and duration of the bombardment affect the surface roughness characteristics. In our case, AL2O3 (aluminum oxide) is used, followed by acid etching [hydrochloric acid (HCl)/sulphuric acid (H2SO4)].
DIF implant surfaces are treated using the certified SLA method. What exactly is this surface treatment method?
The preparation of the future dental implant is a semi-finished product - a titanium screw. Further processing of the workpiece in several stages is necessary to obtain a dental implant from it.
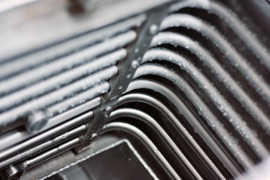
IMPLANT WORKPIECE CLEANING
Stage 1
IMPLANT WORKPIECE CLEANING
Step 1: The process is carried out in a special vibroapparatus using a chemical catalyst to remove metal chips and oil.
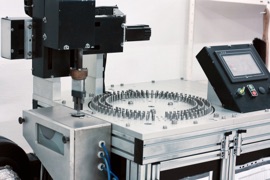
SANDBLASTING
STAGE 2
SANDBLASTING
SLA – 1st step: this kind of treatment is carried out in a sandblasting machine by bombarding the surface of titanium workpiece under high pressure to give its surface a roughness of 1.7 Ra.

ACID ETCHING
STAGE 3
ACID ETCHING
The implant workpiece is immersed in acid, followed by an increase in temperature.
SANDBLASTING
STAGE 4
SANDBLASTING
SLA – 2nd step: repeated bombardment of the surface of the implant preform after acid etching.
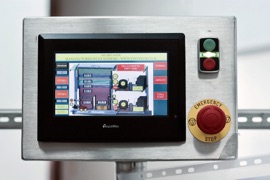
RE-REFINING OF THE IMPLANT PREFORM
STAGE 5
RE-REFINING OF THE IMPLANT PREFORM
2nd step: refining of inclusions on the workpiece surface in the form of contaminating residual particles after final sandblasting.
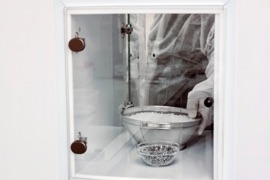
IMPLANT PREFORM STERILIZATION
STAGE 6
IMPLANT PREFORM STERILIZATION
This is the final phase of implant preform treatment, which takes place in a special sterile room, where the packaged product is exposed to gamma radiation.
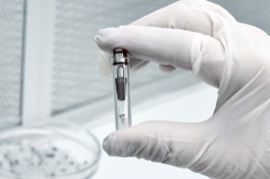
DENTAL IMPLANT PACKAGING
STAGE 7
DENTAL IMPLANT PACKAGING
1st step: finished implant is placed together with the implant-driver and the cover screw into the PET thermoformed tray.
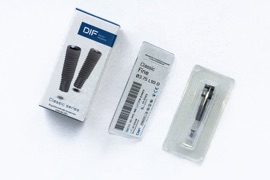
DENTAL IMPLANT PACKAGING
STAGE 6
DENTAL IMPLANT PACKAGING
2nd step: the implant is sealed with a Taivek 1073B membrane cover in a special press machine at 120-130 degrees Celsius, then packed in a box with a sticker (marking) for the doctor and patient.
QUALITY CONTROL
1. All the manufactured products must fully be in accordance with the original technical drawing. If there is a discrepancy in the quality control process, the product is discarded.
2.The cutting tool of the lathe has its endurance. The use of tools that have run out of resources significantly affects the quality of the final product, which results in a large number of defects – i.e. additional costs. DIF is not interested to incur unnecessary costs, thereby increasing the cost of products, so there is constant control over the resource of all production tools.
3. Each tenth product leaving the machine is fully inspected for compliance with the technical drawing. If a discrepancy is detected in the drawing, the entire production line is stopped to identify the cause.
4. After refining is carried out, all medical devices are re-checked electronically.
300
products per hour go through quality control
Today the production of dental implants and their components due to technology, compliance with surface treatment requirements, high quality control at all stages has minimized errors and defects in the production process.
Maintaining the highest technological level for many years, DIF continues to successfully produce premium quality products.